Then lofting day arrived, and in five hours two 3D boat skeletons magically appeared out of all the flat lumber around the shop. We were setting up the laser, re-working the levelness of the strong back, hanging plumb lines from the ceiling, digging around for the right length screws. Anyways the learning curve was: the first boat took 4 hours to set up and the second boat took one hour. I do believe we are the ONLY guys building 2 boats side by side.
At the end of the day it was hard not to sit and stare/contemplate our new boats forming right before our eyes.
The next day I started installing the stringers. Using a tiny sanding drum I relived the excess lumber so the stringer would fit flush with the bulkhead. Now I need to shape all the bulkheads and stringers so the plywood skin fits smoothly over them.
Also, I glassed up the skeg mold, faired it smooth, and coated it with white epoxy.
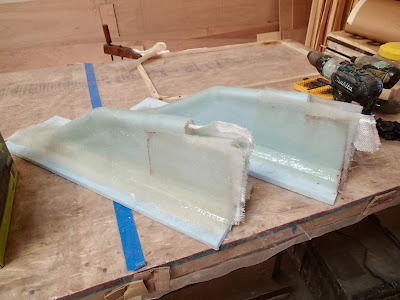
I made lunch on the galley stove, trying out various brands of food.
Repolished some of the stainless steel. Some were polished on the wrong side, and some were just truly awful from the factory.
For fun, I clamped everything together to get a feel of her size.
Next are pictures of the rudder getting its epoxy and glass.
Strong back into lofting.
First stringer
Second stringer and keel oak.
Third stringer
No comments:
Post a Comment